Group Leader Navigation application developed to improve the efficiency of manager operations at manufacturing sites.
Aisin Corporation
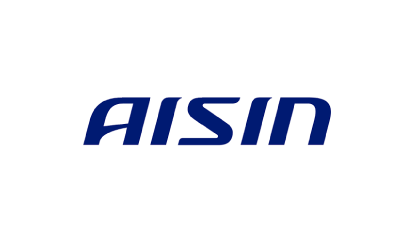
- Company name
- Aisin Corporation
- Address
- 2-1 Asahi-machi, Kariya, Aichi
- URL
- https://www.aisin.com/en/
- Businesses
- Manufacture and sale of automotive parts and energy- and lifestyle-related products
- Employees
- 35,610 (non-consolidated) 116,649 (consolidated)
- Challenges facing customer
- Interview Movie
- The story behind the introduction
- Feedback from those working on site
- Future expansion and outlook
- Messages from the project leaders
Challenges facing customer
Time was wasted in manager operations at manufacturing sites on simple tasks such as patrols, data recording, input, and transcription, and so on, so there was a desire to reduce simple tasks and utilize resources more effectively by promoting the use of digital tools. An intuitive UI based on the sites was necessary in order to make use of these digital tools at plants where analog methods have been the primary means of working.
Goal of development
In order to develop flexibly and swiftly while incorporating opinions from those on site, we adopted an agile approach and developed our Group Leader Navigation application using the low-code development platform OutSystems. It was first introduced at two plants before being refined and expanded to all domestic plants. Next, the aim is to expand its deployment to the entire Aisin Group, including overseas bases.
Interview Movie
The story behind the introduction
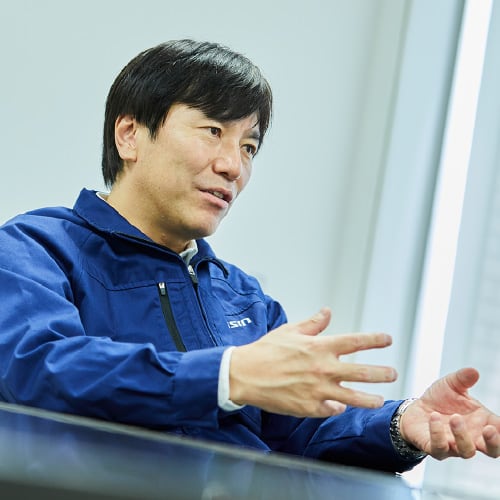
DX Solutions 3 Office,
DX Promotion Department,
Aisin Corporation
We started building an app using an agile approach as we sought something that would truly be easy to use on site.
We have had plans for some time to improve the efficiency of the work of group leaders and other managers. When communication devices between factories switched from PHS to smartphones, we began planning in earnest an application that would allow operations to be completed using smartphones. We wanted to develop something that was easy to use on site at plants, even if it took some time to develop. So, we decided to adopt an agile development approach, incorporating feedback we received from those on site.
Loosely coupling features was a key point to make the app usable at all plants in the future. We were also looking for development that would enable rapid system improvements and changes as well as flexible integration, similar to dividing several functions into microservices and linking them together. Toyota Systems understood this, as well, and has been working closely with the site but with an eye on future development. Even after the development began moving forward, I felt relief that they were working as a single team with our DX Promotion Department toward the same goal.
Feedback from those working on site
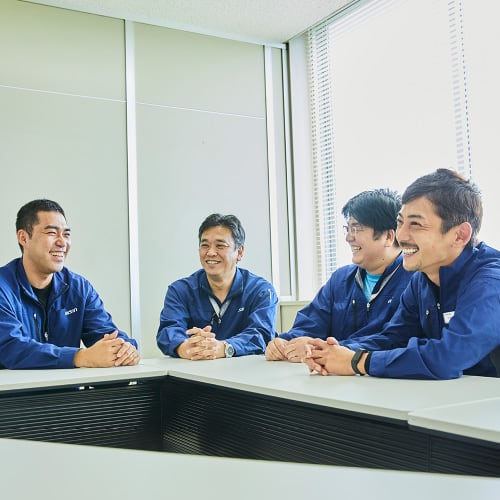
Asato Tomita,
Best Standards Formulation Group,
Manufacturing Technology Office,
Tahara Plant,
Aisin CorporationSatoshi Maeda, Chief,
Skill Development and Blade Tool Improvement Section,
2nd Processing and Manufacturing OfficeKoki Ishida, Foreman
Naoki Goto, Group Leader, 1st Section,
T Aluminum/LA Ring Processing Section,
2nd Processing and Manufacturing Office
Closely observing the plant and experiencing the challenges for themselves.
Rapid and accurate development based on a deep understanding of the site.
For this development, Kadota and his team at Toyota Systems spent three full days on site with the group leader, experiencing the work for themselves. In the event of an abnormality, it takes about 20 minutes to travel to and from a station or office to write the results of the corrective actions on the Abnormality Notification Board. They walked this distance together. Having the Toyota Systems team experience the challenges on site and feel firsthand where there was room for greater efficiency and improvement likely helped accelerate development later on.
By having that understanding of the site, it was easy to consult on small matters. Solutions were quick, and the development progressed with both parties in sync. And if anything, Toyota Systems looked at areas that our employees on site had not noticed and gave us great suggestions. Development advanced as swiftly as it did because they took all requests and consultations seriously, always stayed close, and responded quickly. In addition, Toyota Systems provided generous support in the form of informational sessions and support for the introduction of the application. This was reassuring and gave us peace of mind.
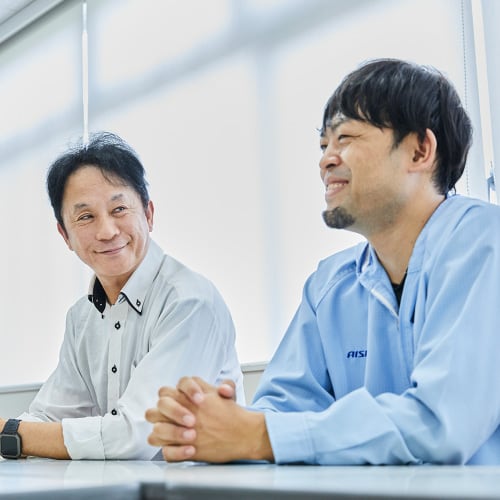
Koichi Suezaki, Manager,
DX Promotion Group,
Manufacturing Technology OfficeYuki Tanaka, Foreman,
1st Work Site, 3rd Section, Computer 1 Section,
Manufacturing Office,
Handa Electronics Plant,
Aisin Corporation
Development as a reassuring single team.
A work culture based on digital tools has gradually taken root on site.
During development, we held regular meetings as a team that consisted of employees from our DX Promotion Department and development support members from Toyota Systems. The speed at which development advanced was quicker than we imagined, and even vaguely communicated requests were often improved upon beyond our expectations. Every time we talked, it was refined into something better.
Those of us with little knowledge likely offered low level opinions and made misguided requests, but because Toyota Systems was always friendly and ready to think of how to make improvements, it was very easy for us to speak our minds. There was a sense that we were building together as a single team, going beyond the conventional boundaries of the company as we aimed for the same goal.
After the introduction of the Group Leader Navigation application, we were able to reduce the amount of time spent inputting and transcribing, reduce time spent moving between areas, and improve the efficiency of our work. This allowed us to increase the amount of time we could spend watching and improving the site. Many of our employees feel the benefits. And not only has work improved; a work culture based on digital tools has also definitely taken root.
Future expansion and outlook
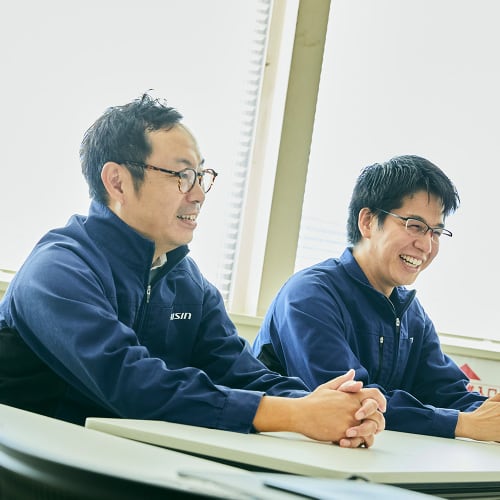
Yasuhisa Kimura,
Seiichi Suzuki,
Chief of 2nd SCM Group,
DX Solutions 3 Office,
DX Promotion Department,
Aisin Corporation
A partner who will worry, think, and sweat alongside you.
A focus on finding reasons and the essence of challenges facilitated smooth solutions.
We first began a trial introduction of the Group Leader Navigation application at two plants, with the goal of eventually introducing it to all plants. Development adopted an agile approach, incorporating feedback from on site to make improvements.
While we wanted to carefully incorporate opinions from those working on site and polish the application into something that was easy to use, there was also the conflict that if too many requests were accepted and the application saw more optimization in some areas, we would be putting the cart before the horse. Sometimes we became lost in maintaining that balance, but Toyota Systems worked together with us to achieve the same goal, worrying, thinking, and communicating in the field as they moved development forward. On top of that, they listened thoroughly to the opinions from those working on site, focused on finding out the reasons and essence of challenges, and led us to solutions. It was very reassuring, and as partners I feel that we were able to build something very positive with them.
Going forward, we hope to take the next step in establishing a culture that is focused on using digital tools such as AI and other latest technologies and the various in-house data based on digital data accumulated on site.
We are very excited to see the site and what new manufacturing work created with Toyota Systems as a single team will look like. Our hope is to use this excitement as a driver for the team and move forward into yet unknown realms.
Messages from the project leaders
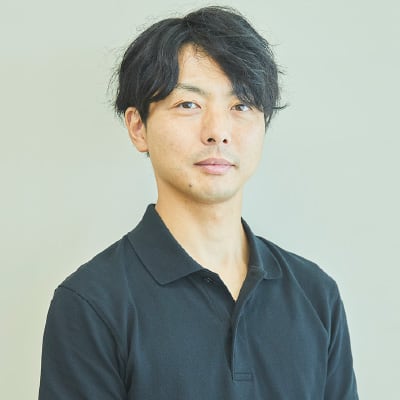
Production Engineering System G,
Engineering Chain Management Reform Department,
Toyota Systems Corporation
By closely observing how the plant functioned for three days, we were able to gain a deeper understanding of the site. We then used that experience in development support.
With this project, we adopted an agile approach using OutSystems. But for this to be successful, it is essential that we have those in the field try it in earnest and give us meaningful feedback we can use in the next iteration. While listening thoroughly to opinions from those working on site, we implemented development support with an awareness of developing an application that could be expanded to work at all plants.
We will continue to strive to support Aisin in transforming its manufacturing sites digitally.
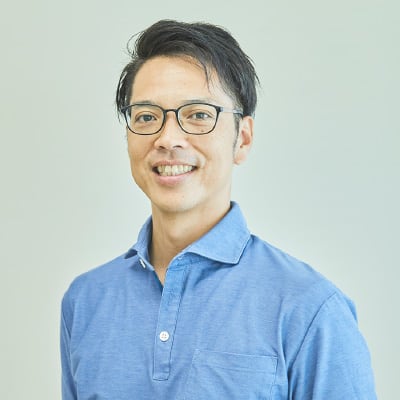
Promotion G,
Account Business Department,
Toyota Systems Corporation
(On-Site Support,
DX Corporate Planning Office,
DX Management Department,
Aisin Corporation)
Currently, I am stationed on-site in Aisin's DX Corporate Planning Office and am involved in various DX promotion activities, including the development of the Group Leader Navigation application.
One of Toyota Systems' strengths is our ability to provide comprehensive support across a wide range of areas—not only app development but also infrastructure such as our network team and our data analysis team.
We always keep in mind what DX should be and what we need to do now to support manufacturing plants. As we do this, we support further DX promotion such as optimal plant networks and AI utilization by connecting Aisin and Toyota Systems' respective departments.