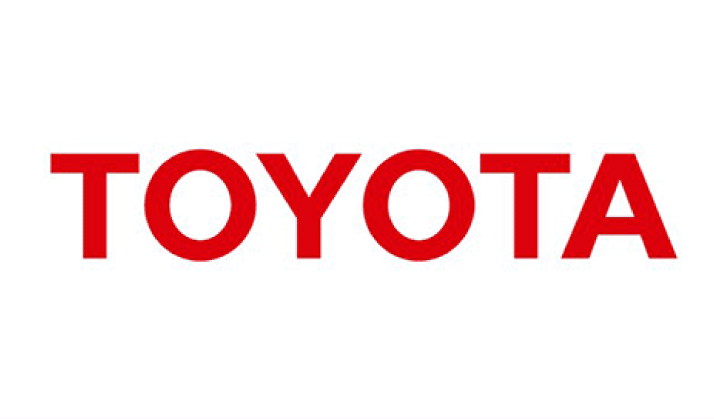
- 社名
- トヨタ自動車株式会社
- 所在地
- 愛知県豊田市トヨタ町1番地
- URL
- https://global.toyota/jp/
- 業種
- 自動車の生産・販売
- 従業員規模
- 70,000人以上
お客様の課題
時代の流れとともに、車両開発のリードタイムが短くなっている。図面と現物を見比べながら実施するような時間のかかる作業の効率化や、現物がないと確認できない設備改造の早期着手が必要となっていた。
導入効果
現状を打破するべくデジタルツール導入を検討。ボデーのスポット溶接において、実車にARでデータを重ねチェック作業を効率化。また、設備改造に必要な部品を3Dデータに置き換えることで成立性を確認し、期間を短縮できた。
採用の理由
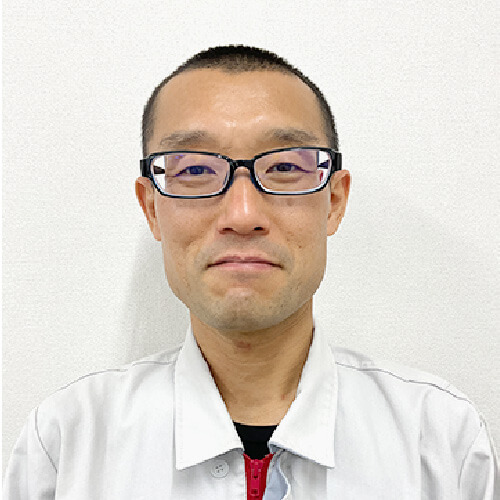
車体製造技術部 プレス技術室
デジタル解析グループ 主任
斎藤 秀樹様
リードタイム短縮に向けてARを導入。
コストパフォーマンスの良さも決め手に
自動車業界では、企画から製造までに求められる期間がどんどん短くなっています。私が所属する部署は、デジタルツールを使って仕事をより簡単にすることを目標としていますが、そういった背景もあり、デジタル技術の必要性をより強く感じていました。そんな中でAR技術を知り、実用可能か検証を進めました。実際に導入となると、操作性やコストなどの課題が出てきますが、トヨタシステムズさんからご提案いただいたARツールは、機能面はもちろん、他社製品と比較してコストパフォーマンスが良いところに魅力を感じました。
導入までの流れ
-
2021年12月
プロジェクトスケジュールに合わせて断続的にトライ
-
2022年5月
効果が見込めたため、本格的に導入開始
導入効果
現物がないと作業がストップしていた工程も
ARに置き換えることでロスタイムを削減
ARは、板金同士のスポット溶接が正しい位置にあるか、漏れがないかの確認作業と、新車を生産する際に実施する設備改造の2箇所で採用しています。溶接の確認作業では、車両1台あたり4~5千点あるスポット打点を人の目とスケールで確認していましたが、ARによってタブレット越しに一目瞭然に確認できるようになりました。設備改造では、これまでは新しく必要な部品をすべて用意し、実際に作ってみて問題がないか確認していましたが、それを3Dデータに置き換えて容易に確認ができるようになりました。これにより、部品が揃わないと着手できなかった作業や作り直しのロスタイムを削減できました。
今後の展開・展望
トヨタシステムズさんと密に連携し、
よりスピーディーな開発をしていきたい
実際に使ってみて、今まで手作業で確認していた工程にARを導入するのは非常に有効だと感じました。現在は、更に効率の良い使い方や新しく適用できる工程がないか探っているところです。ゆくゆくは海外事業や提携企業様とのやり取りにも活用できればと思っています。幅広く簡単に使えるツールにしていくために、トヨタシステムズさんとより密に連携し、スピーディな問題解決、改良をしていきたいですね。最新のデジタル・IT戦略に強いトヨタシステムズさんの特長を生かし、ツールだけに留まらないソリューションの提案も期待しています。
担当メッセージ
今回ARツールを導入いただいたスポット溶接のチェック作業では、実物とデジタルデータの位置を精度良く合わせることが重要です。その点において、本ソリューションが持つ認識技術の強みが発揮されています。また、当社サービスはお客様側のサーバー準備が不要で、ライセンス数を最小限から導入できるなど、コストが抑えられる点においてもご評価をいただきました。車両開発コストの低減やリードタイムの短縮など、年々高まるご要望に応えるため、トヨタ自動車様とは密接なコミュニケーションを取りながら、ARのさらなる活用をご提案していきます。
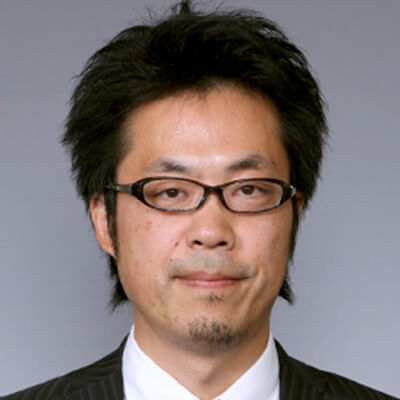
生産デジタル展開部
DXソリューション3G
主幹 菊地 英幸