Evaluating color quality without applying paint-A first-of-its-kind technology from Toyota
Color is responsible for the first impression a car makes and is therefore an important point of product competitiveness. Just as color trends in the fashion industry change every year, trendy colors also change in the automotive industry.
However, the road to sale on the market is not an easy one. Factors such as the composition of the paint, the painting method, and the environment are intricately intertwined. As it was conventionally necessary to apply paint physically and evaluate and confirm the quality, and rework was also necessary at times, meaning it took considerable time to develop new colors.
Toyota Systems therefore entered the field of paint at Toyota Motor Corporation and examined solutions together with personnel working on site. By digitalizing the process-from color production to measurement-it became possible to improve quality and quantity over short periods of time by evaluating quality without applying paint physically.
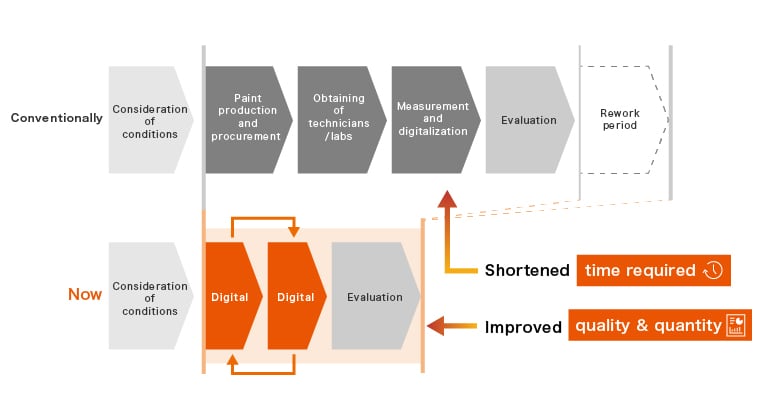
Paint Appearance and color variability
The first step in creating a new color is to set a goal for that color. The next step is the creation of a paint recipe. Various factors are intricately involved in this; they include how to blend and dilute the paint, the robot conditions when applying the paint, the temperature and humidity of the booth, and the composition of the paint film. So, even if using the same recipe, if the type of car body or the place where the car is assembled changes, the color after application will look different.
We have started to develop technology for the two factors that play major roles in this difference in colors. The first factor is Paint Appearance , or the fine irregularities found in the surface that give it its luxurious appearance. The second factor is color variability, which occurs during mass production at plants.
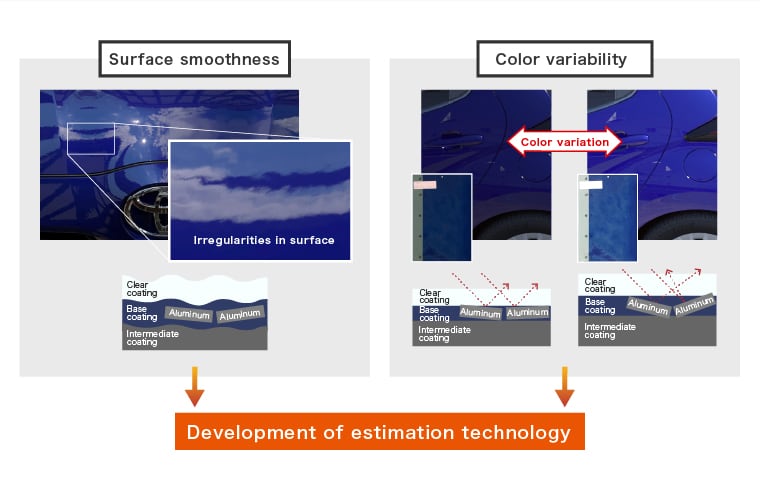
Digitizing the complexity of the painting process and the know-how of experienced workers
There are two key points when developing the technology. The first is creating data to explain the complex factors of the painting process. And the second is how to incorporate the know-how of experienced workers on site gained over the years.
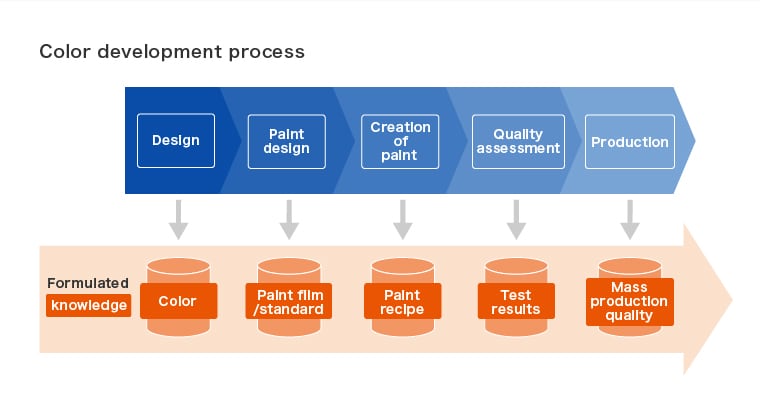
In creating the data, we focused on the color development process. For factors in each process, we leveraged Toyota Systems' 20 years of IT support in the field of paint and color to create a dataset that links information on design, materials, quality evaluation , and mass production. This is basic data for analysis so that the technology can be used to handle the multiplication of various factors.
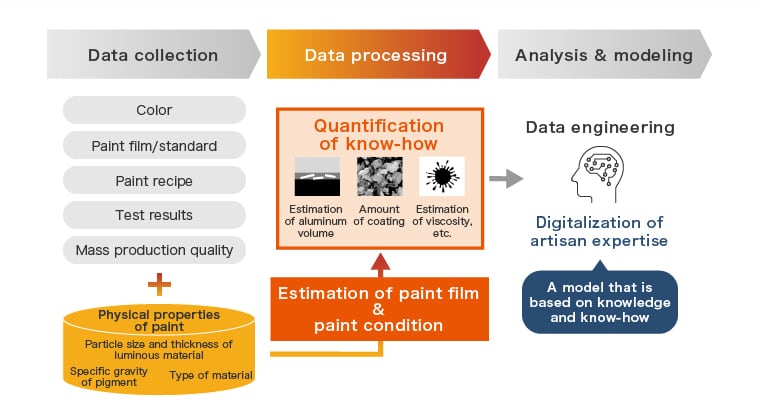
A paint simulation system that reproduces color and paint quality with precision
After repeated trial and error, we developed a paint simulation system. Based on the data incorporated by AI, a visualization of the actual application is reproduced based on the paint recipe and the car body model.
By replacing the method of assessment with a digital one, we were able to shorten the time needed when compared to the work hours required by the conventional method. The evaluation to assess it digitally has begun depending on the difficulty of the color.
This first-of-its-kind technology has already been applied for patent in Japan and overseas (US and China) and has been presented at the International Conference on Automotive Painting Technology.
Delivering joy to our customers
Digitalizing the quality evaluation in the painting process allows for high-quality, trendy colors to be made available quickly. This in turn helps deliver joy to our customers.
We will continue to use AI, VR, and other digital technologies to improve our technical capabilities on a daily basis so that we can help increase production efficiency and customer satisfaction.